Talend customers
Learn from the companies that are leading the way and generating real value by prioritizing data health
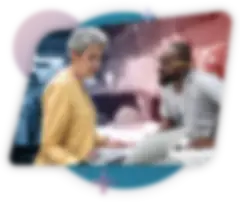
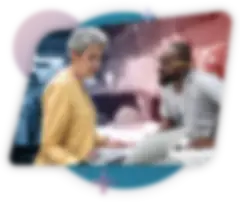
Featured success stories


Brewing up the best consumer experience


Delivering analytics at lightning speed with Talend and AWS
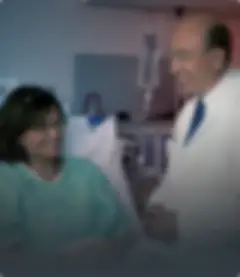
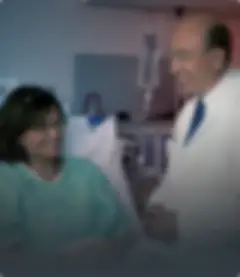
Building data-enabled preventative healthcare with Talend
Experience breakthroughs in data health
Products Region Industry